CREATING A FUTURE FREE FROM COMMERCIAL WAstE
My adidas zero waste project imagined a future where limited resources entailed new laws on fabric usage. Conglomerations such as @adidasoriginals / @adidasskateboarding are forced to resort to zero waste practices in order to stay profitable. This meant finding zero waste patterns for loved classics and a new way to make these shapes unique.
My conceptual stage remained analogue, using photography of skate spots at home with friends to create textural montages which would inspire material and outfit choices.
Once my colour way was decided, I used cutouts from magazines to inform how my photographs could be used as prints or embellished details on the final product.
This is a time consuming but extremely satisfying way to create textile designs and let my pattern remain true to classic functional silhouettes that are tried and tested by skateboarders already!
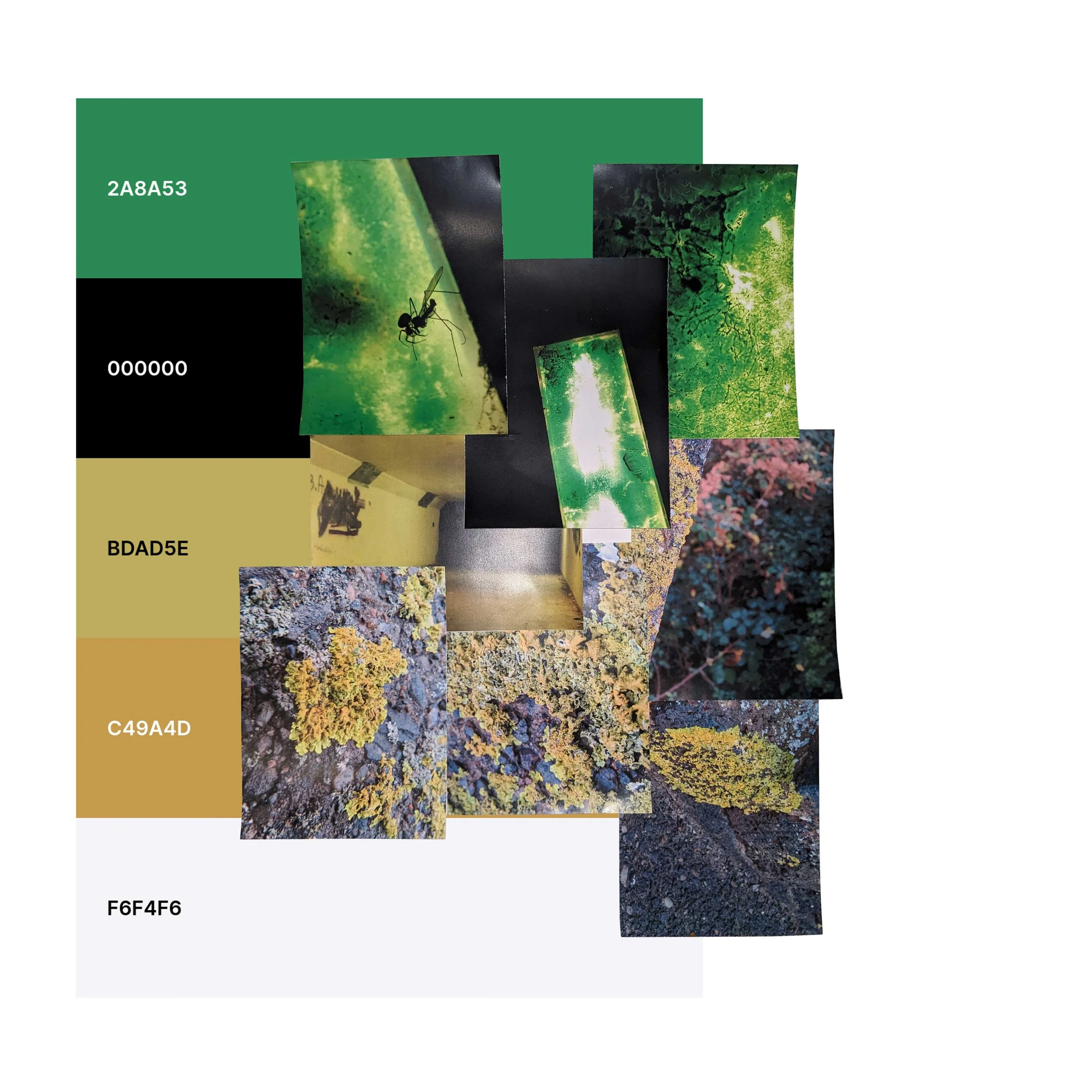

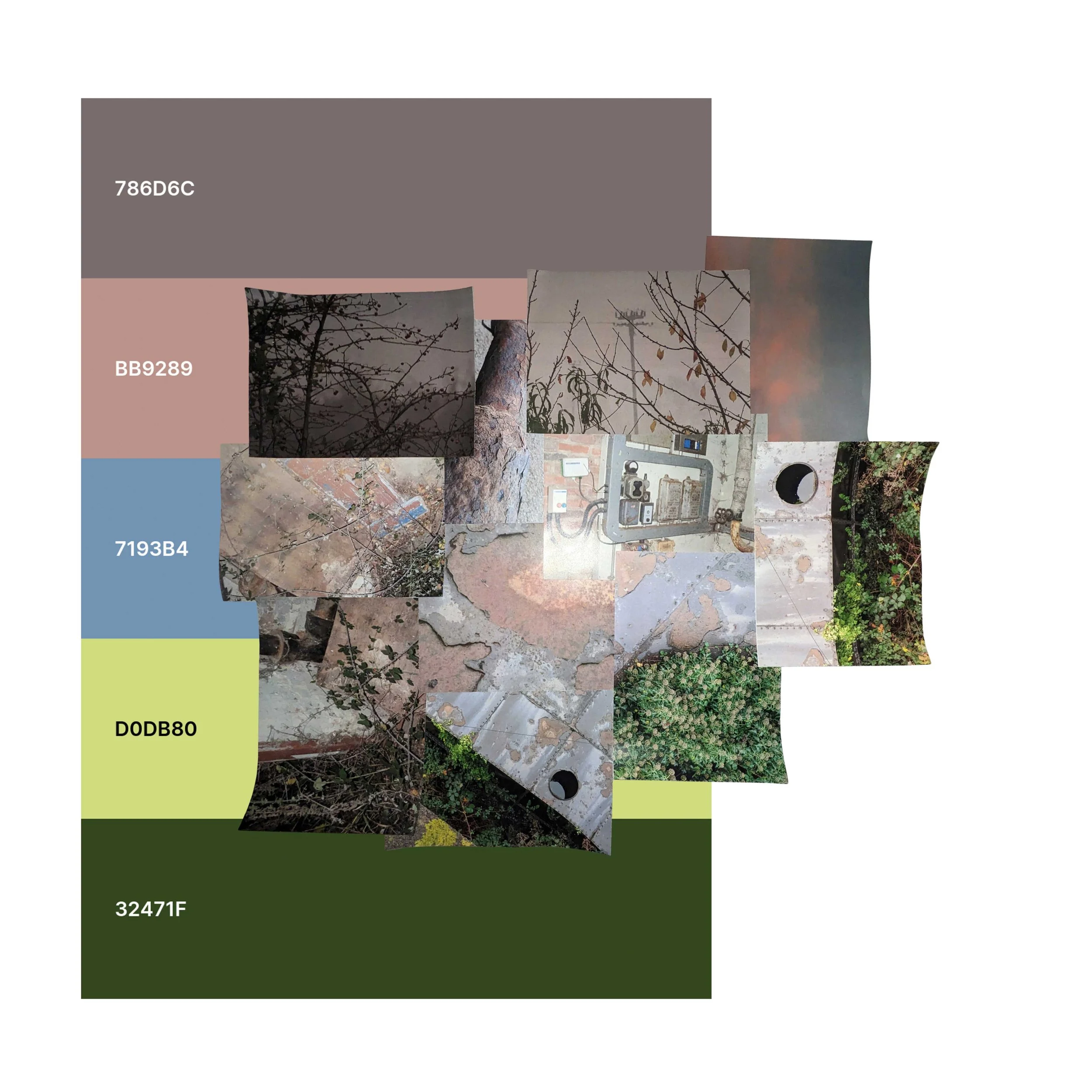
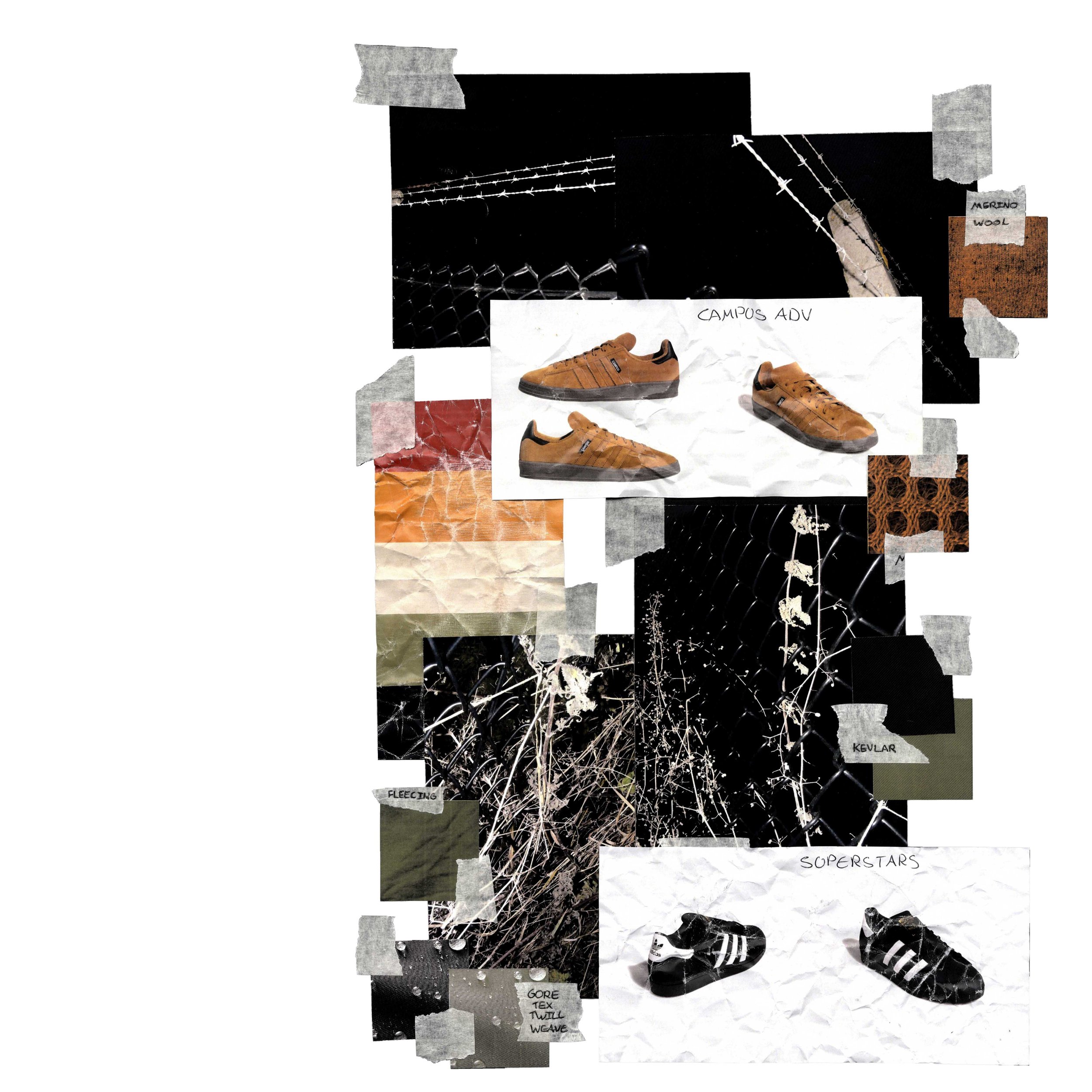

discovering zero waste
This experience marked my first exploration into zero waste pattern cutting, utilizing a technique known as jigsaw cutting. This method allows for a seamless arrangement where each piece fits together like a jigsaw puzzle. I began by sketching the desired silhouette for the main body shape and then creatively used the excess fabric to incorporate design elements, including pockets and the iconic Adidas three stripes.
Additionally, this project introduced me to the CLO 3D software, which proved invaluable for zero waste design. The ability to iterate my ideas digitally, significantly reduced both time and material waste, as I could easily adjust designs without using paper or fabric. The software also enabled me to simulate the overall design, allowing me to evaluate whether elements were proportionate and functional.
Upon completing my initial design, I reassembled the pieces as one would a puzzling jigsaw to ensure the project adhered to zero waste principles. This process led to an interesting creature-like form emerging on the simulation screen. After constructing the first toile, I recognized the need for adjustments, especially in the armpit area. To enhance comfort and flexibility, I added curves to this section. In retrospect, I am inclined to revisit this design with a more pronounced curve, aiming to eliminate straight edges entirely to achieve a baggier and more robust shape.

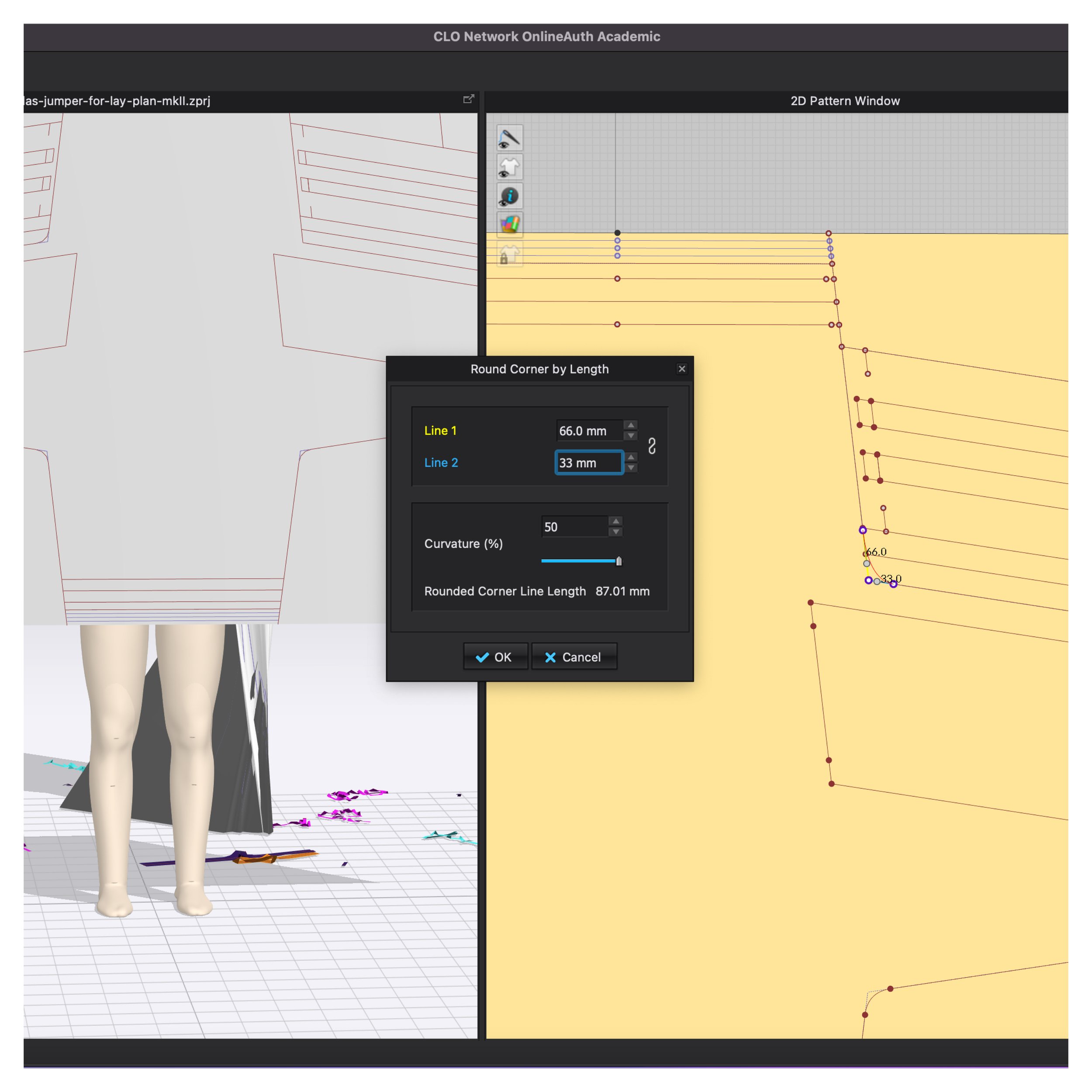
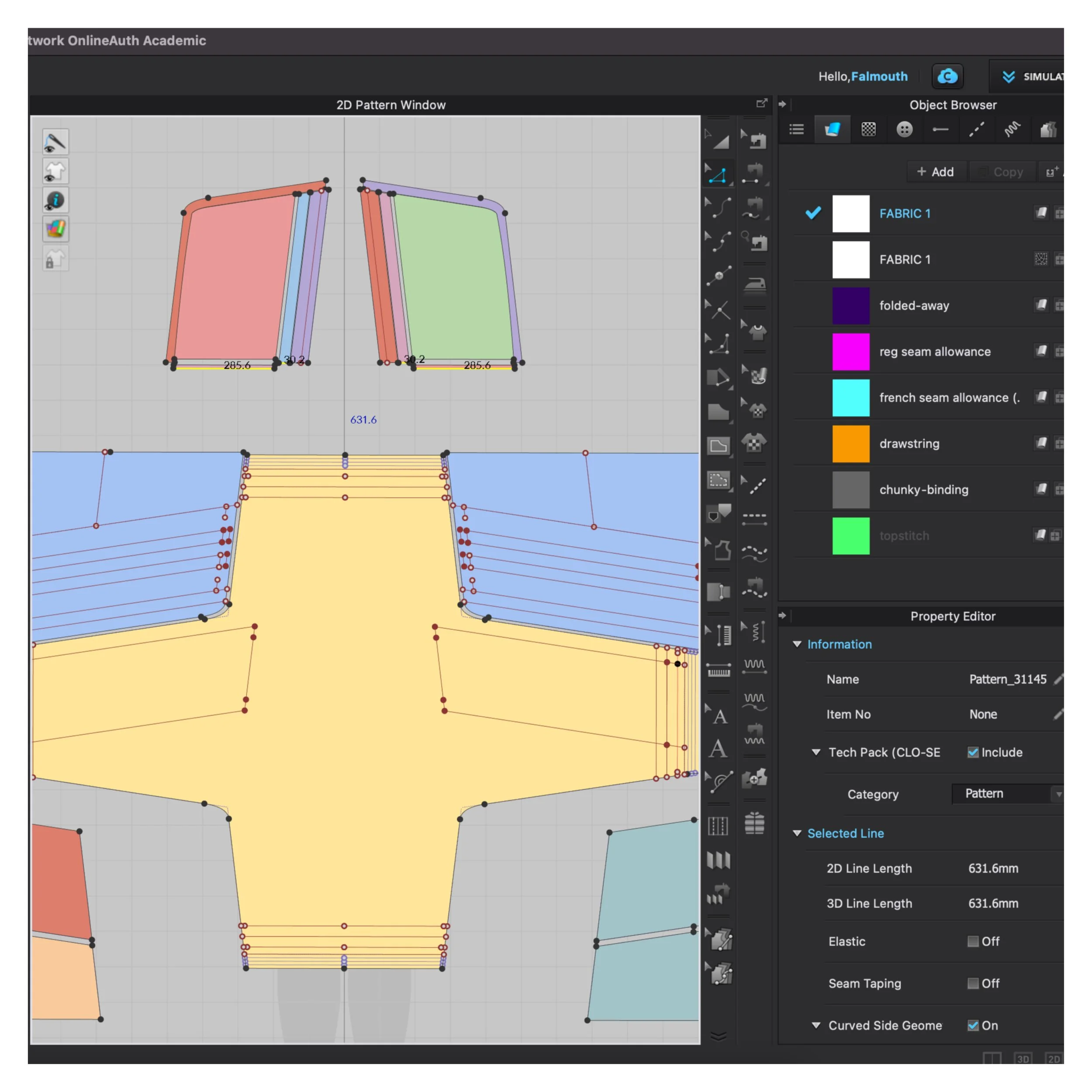
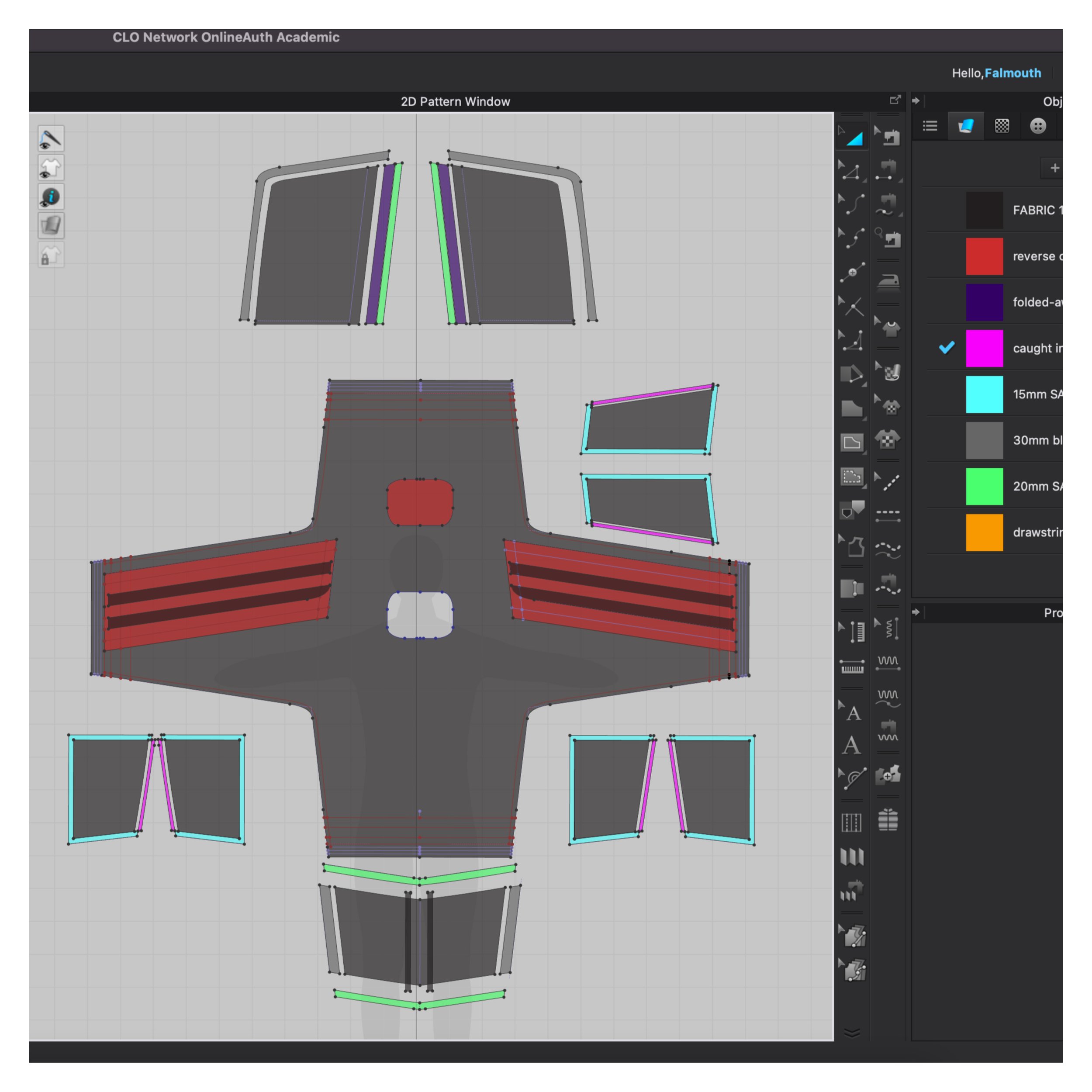
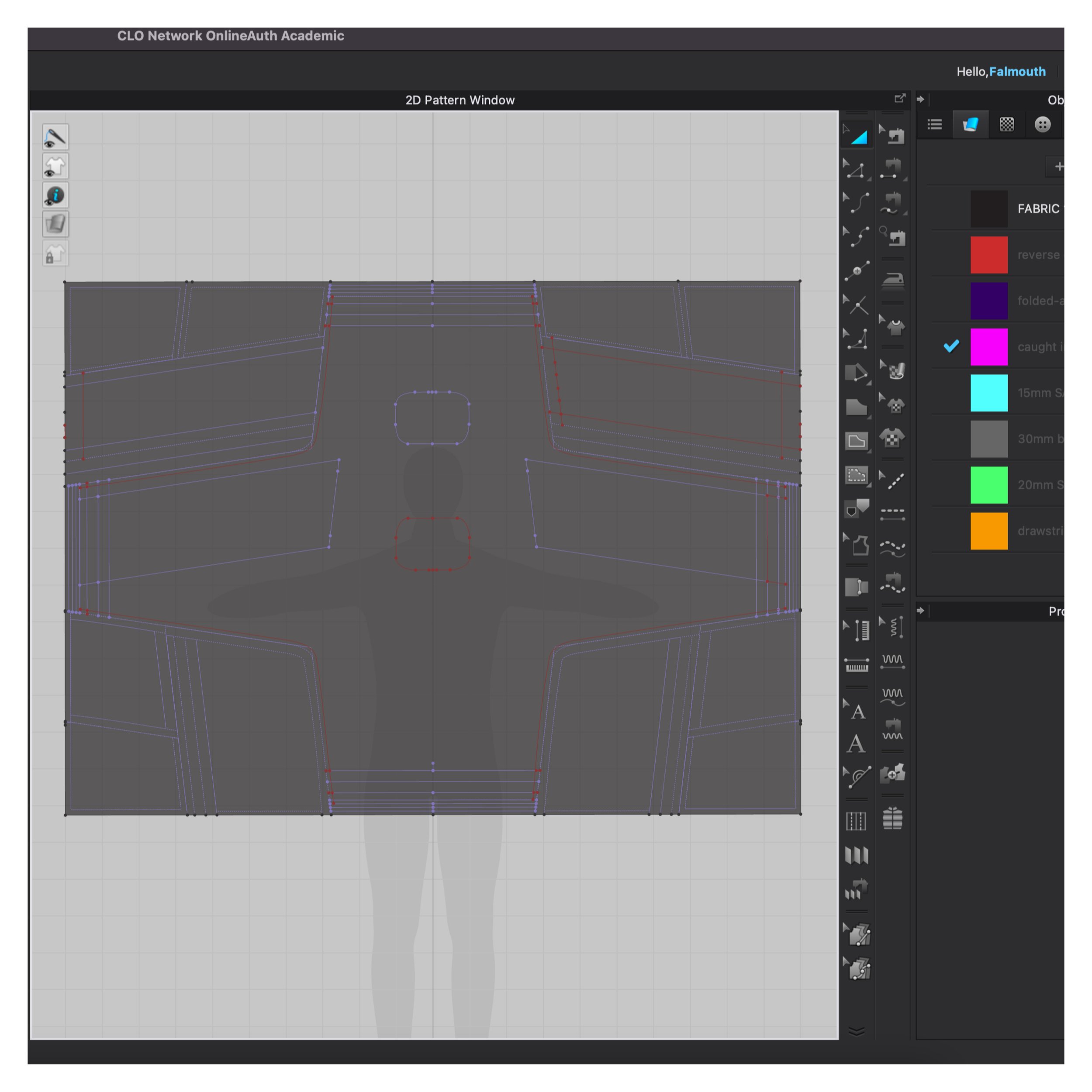
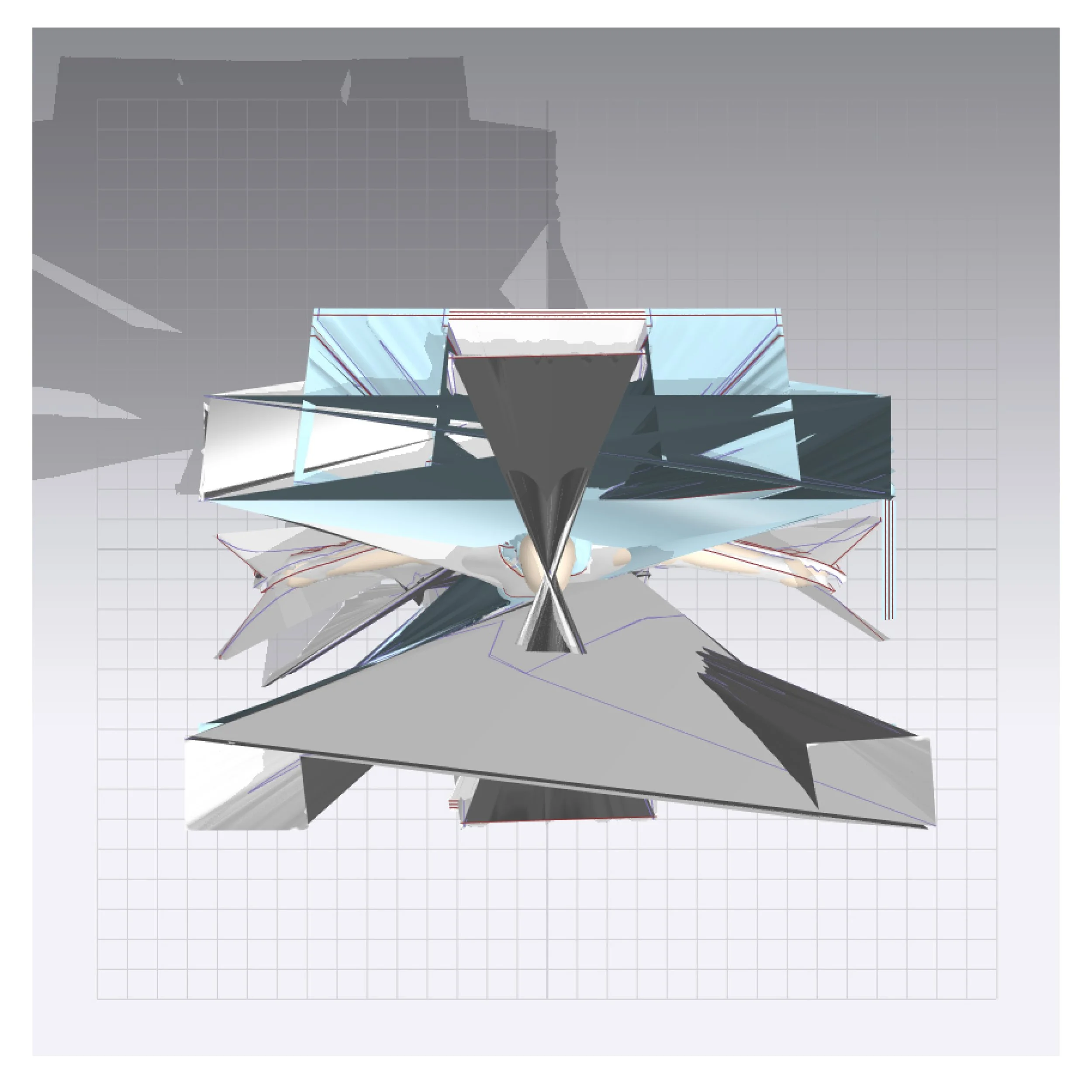
Range Plan
The project demonstrates a thoughtful integration of Illustrator's icon and pattern tools to generate precise quilting patterns and embellishments. Utilizing donated @lavenham stock enhances the project's sustainability while emphasizing innovative design.
The range plan meticulously outlines the technical specifications for the front and back of each garment, derived from carefully crafted zero waste patterns. Although the specific sketches remain confidential for the time being, they reflect a commitment to sustainability and efficiency in fashion design.
Additionally, the range plan details the strategic incorporation of advanced technical fabrics and technologies historically employed by adidas, such as TechFit. This approach aims to develop garments tailored for skateboarders, addressing the challenges posed by increasingly adverse and extreme weather conditions. This foresight positions the collection as relevant and essential in a rapidly evolving outdoor environment.
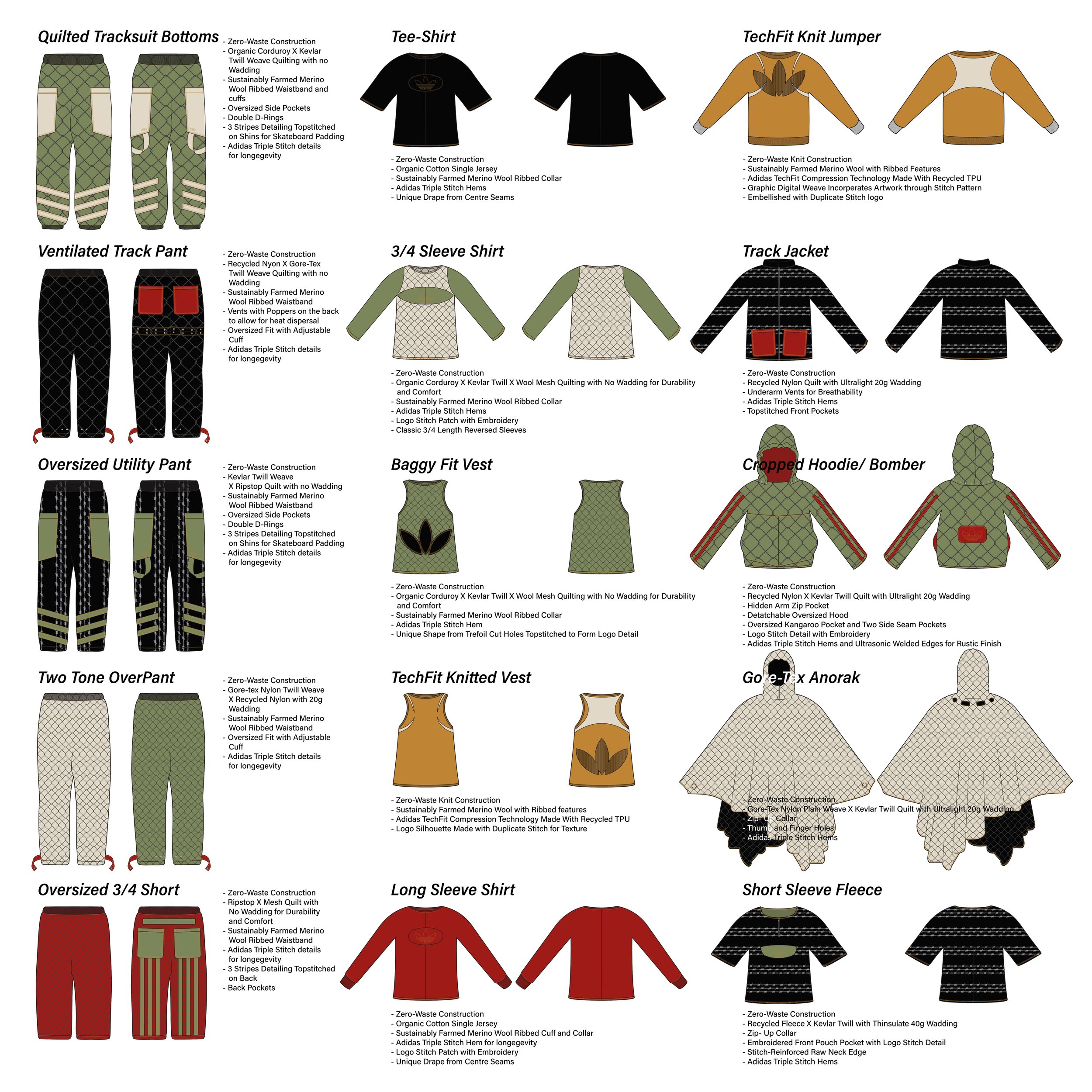
print process
Though I did not print on the garment itself, the print design process was integral to my workflow. I am extrememly interested in this aspect of garment design and I used my own photography to develop textures and prints to be used across all 3 colour scheme options.
I used my spare time to test out freehand ‘irish’ embroidery & the ultrasonic welding machine to add branding anf design elements seen on the back of the hoodie.



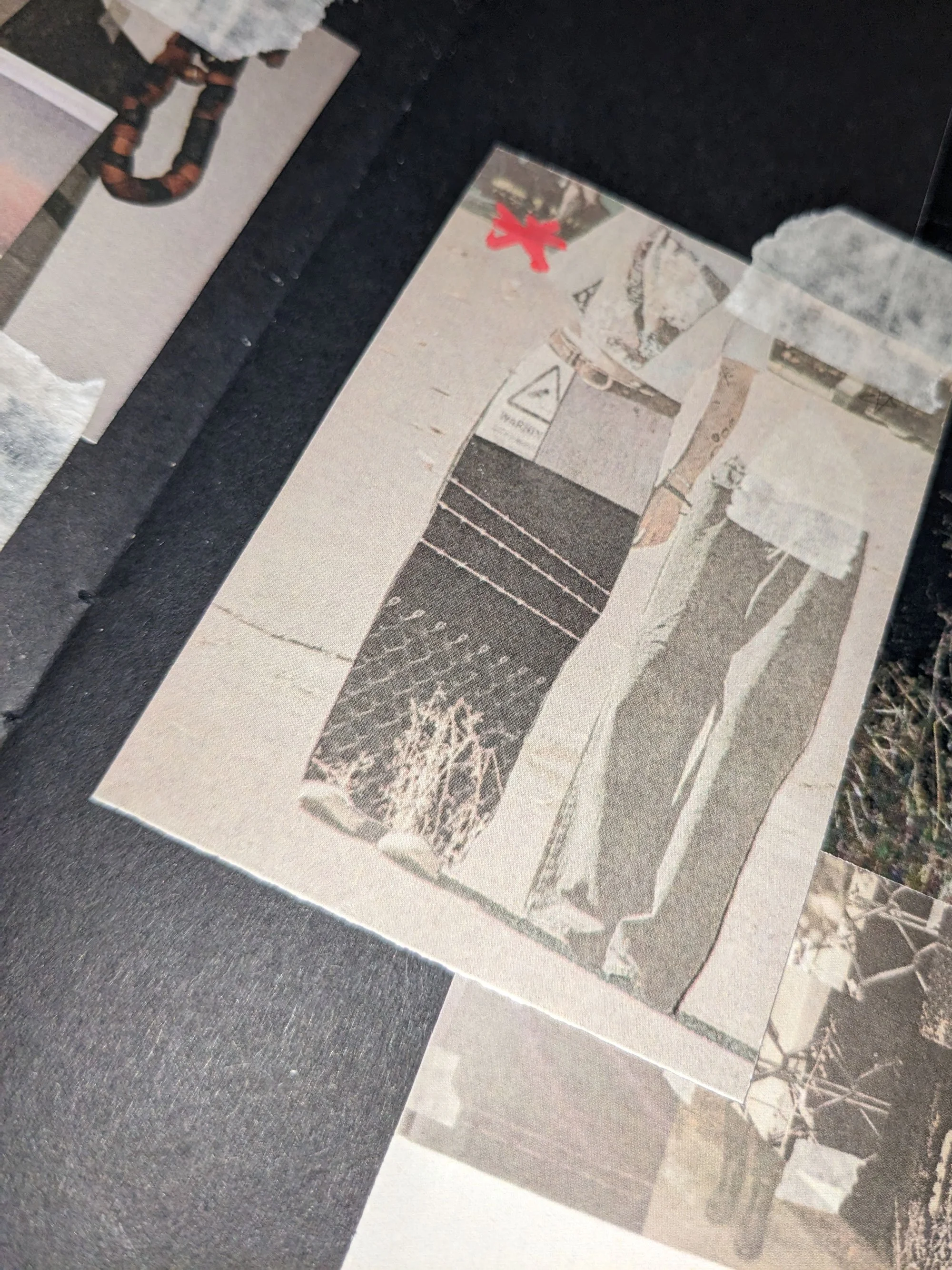
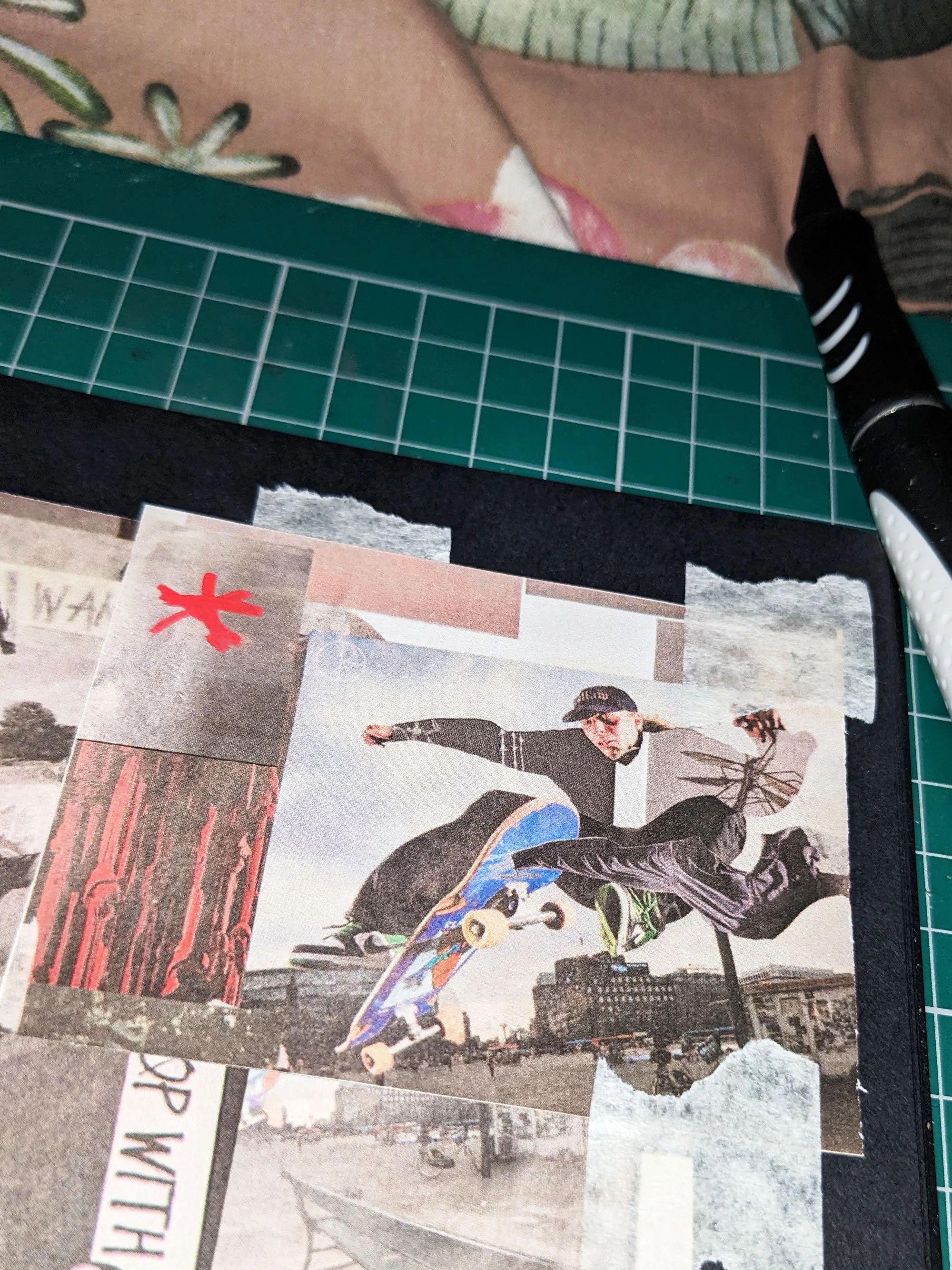
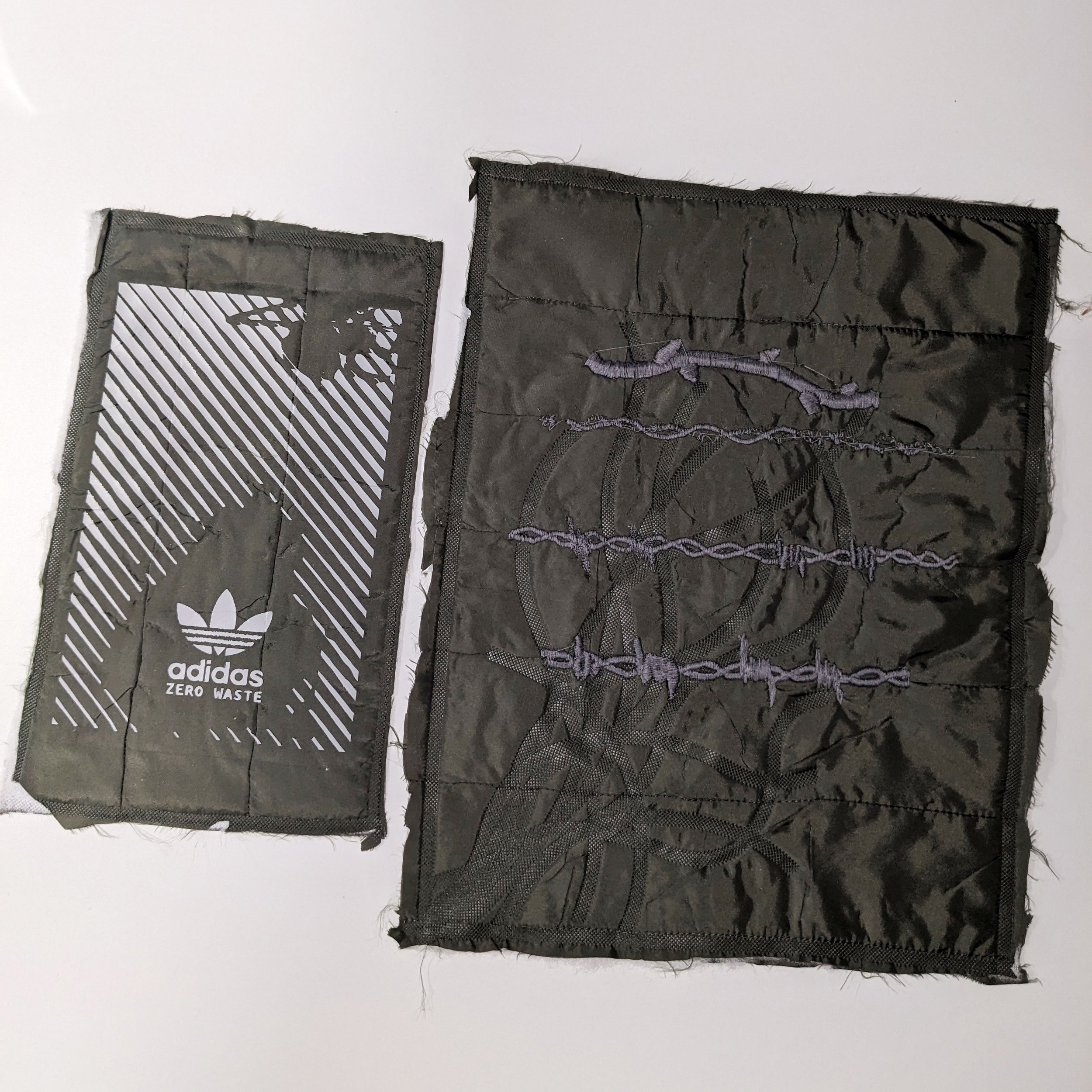
Front, BAck & sides

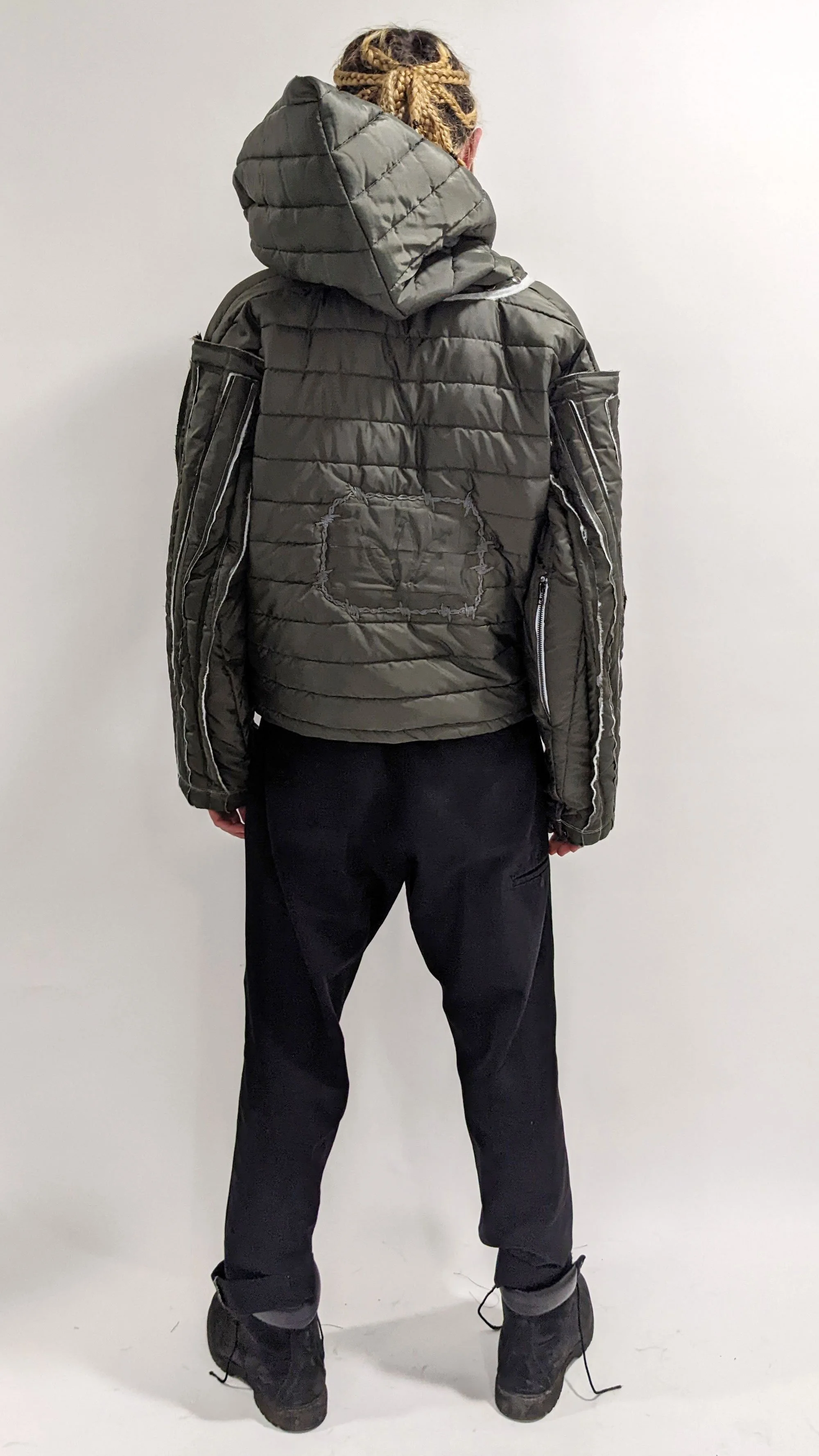
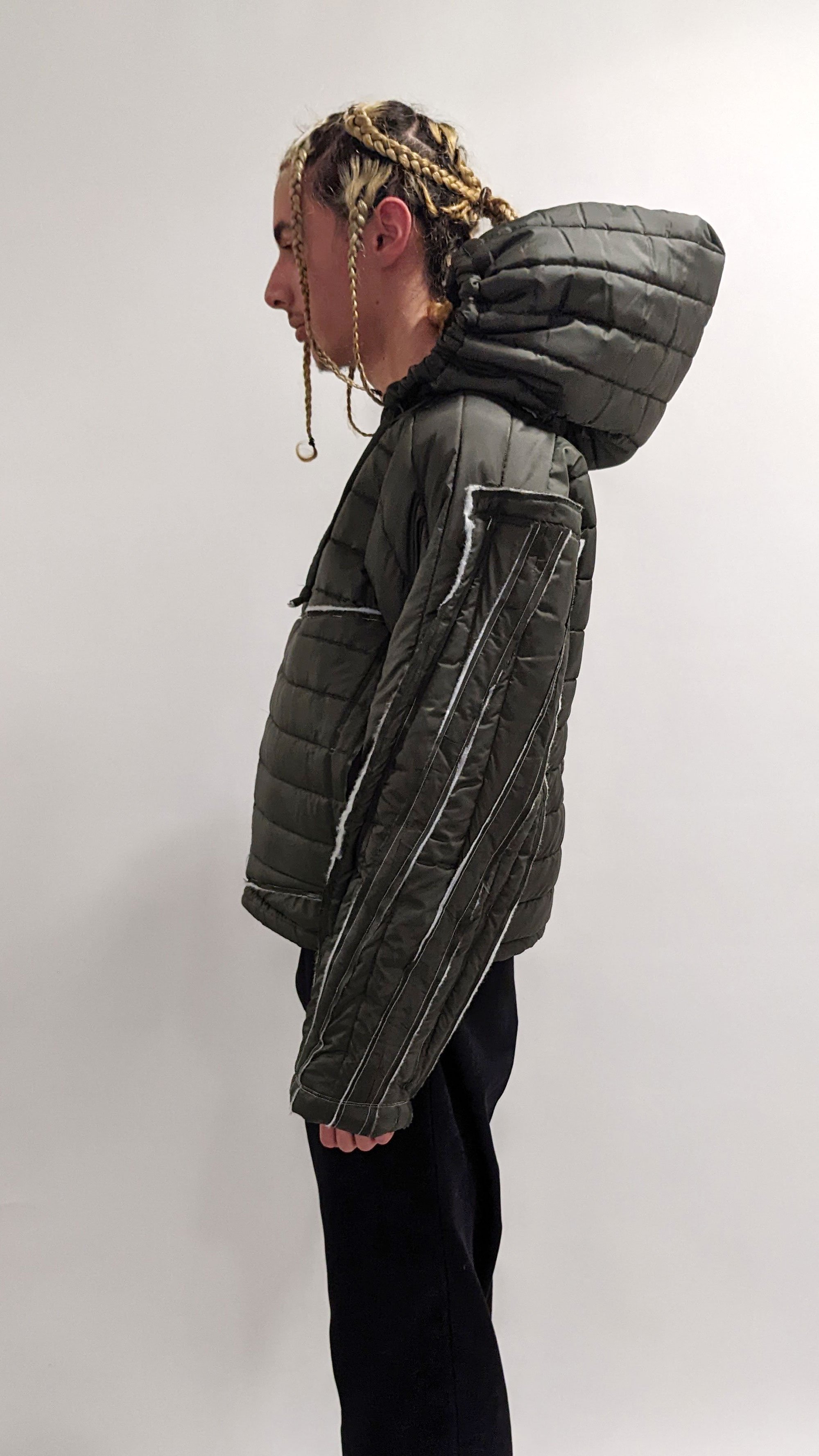
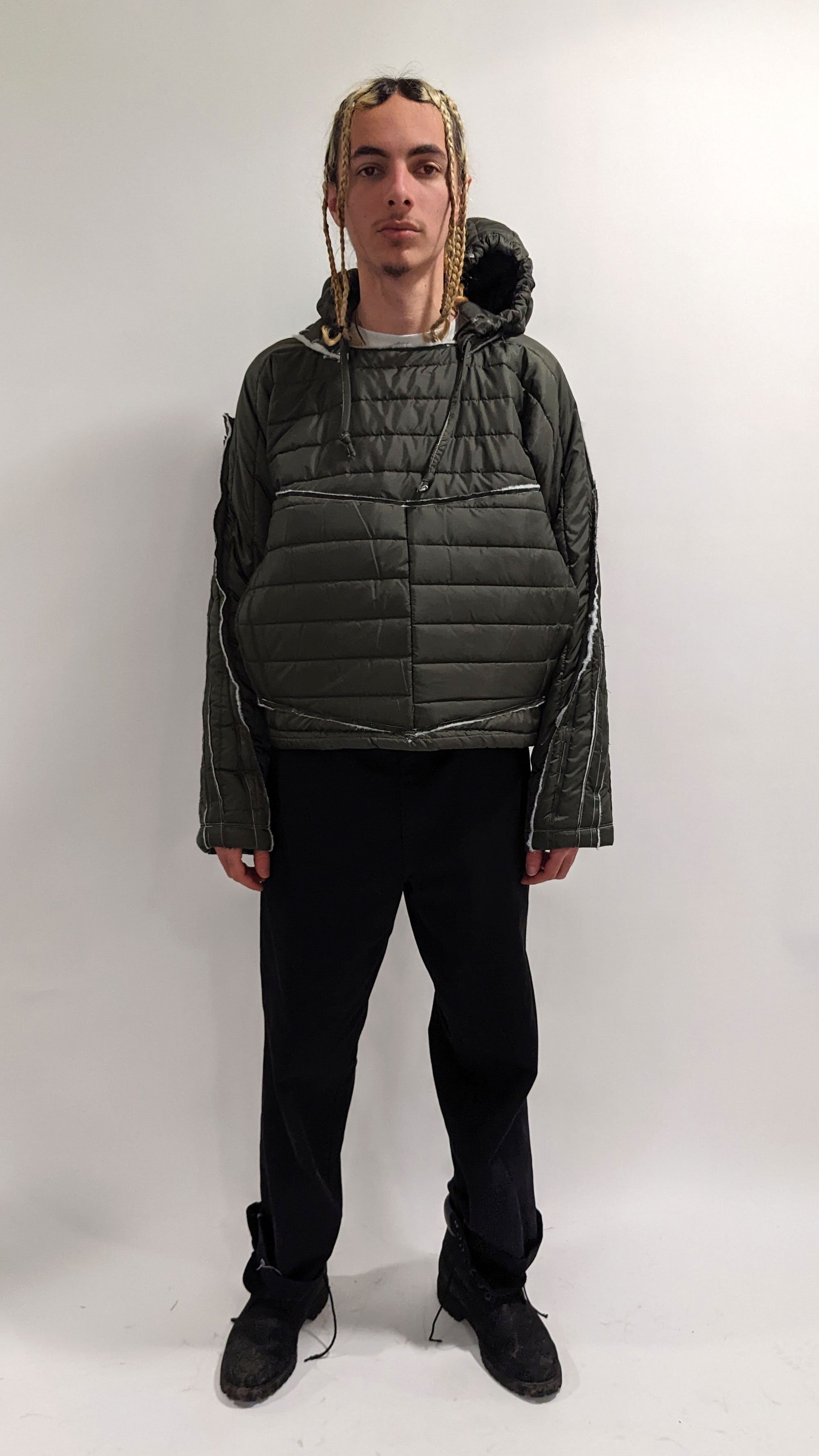
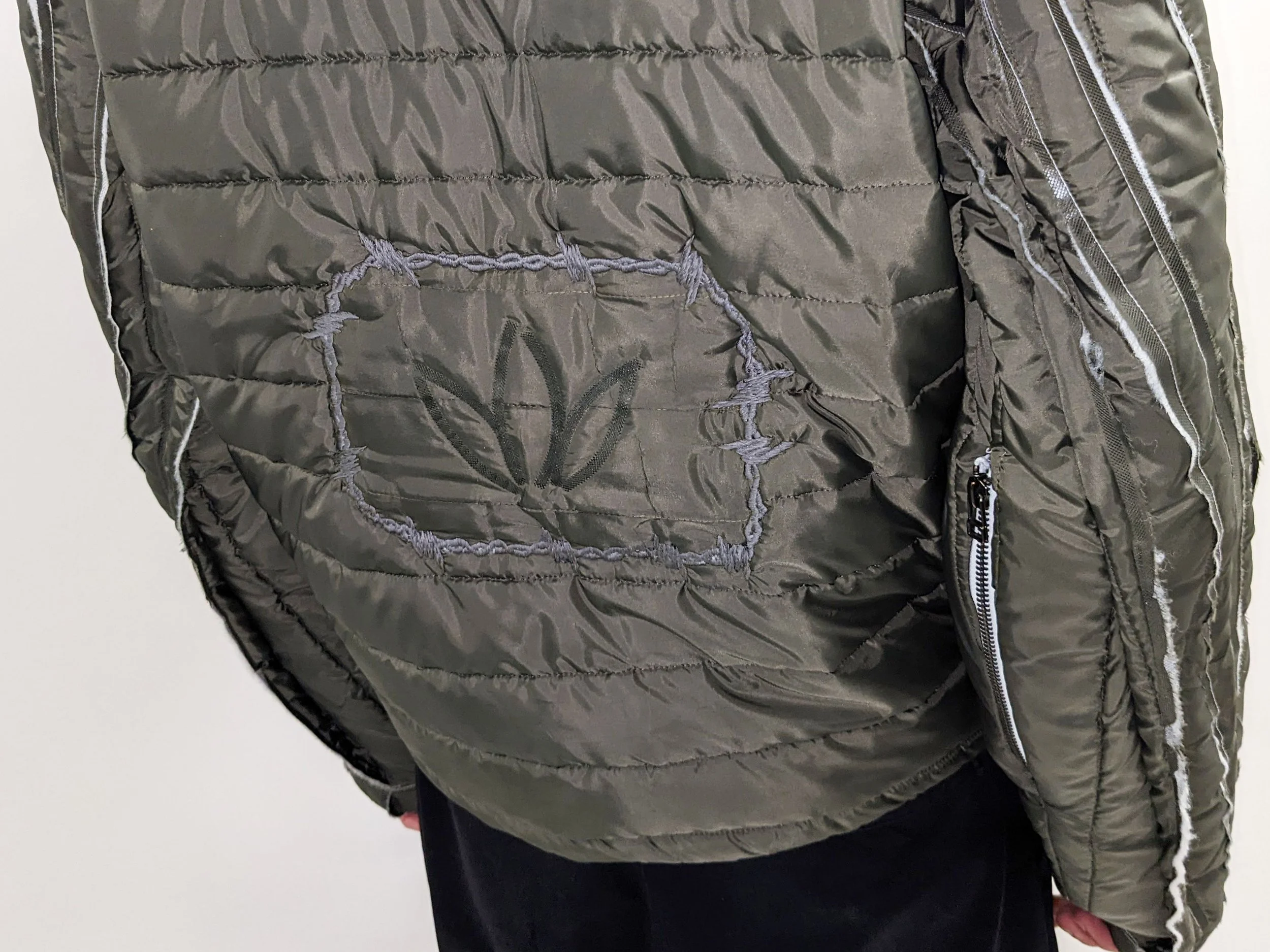

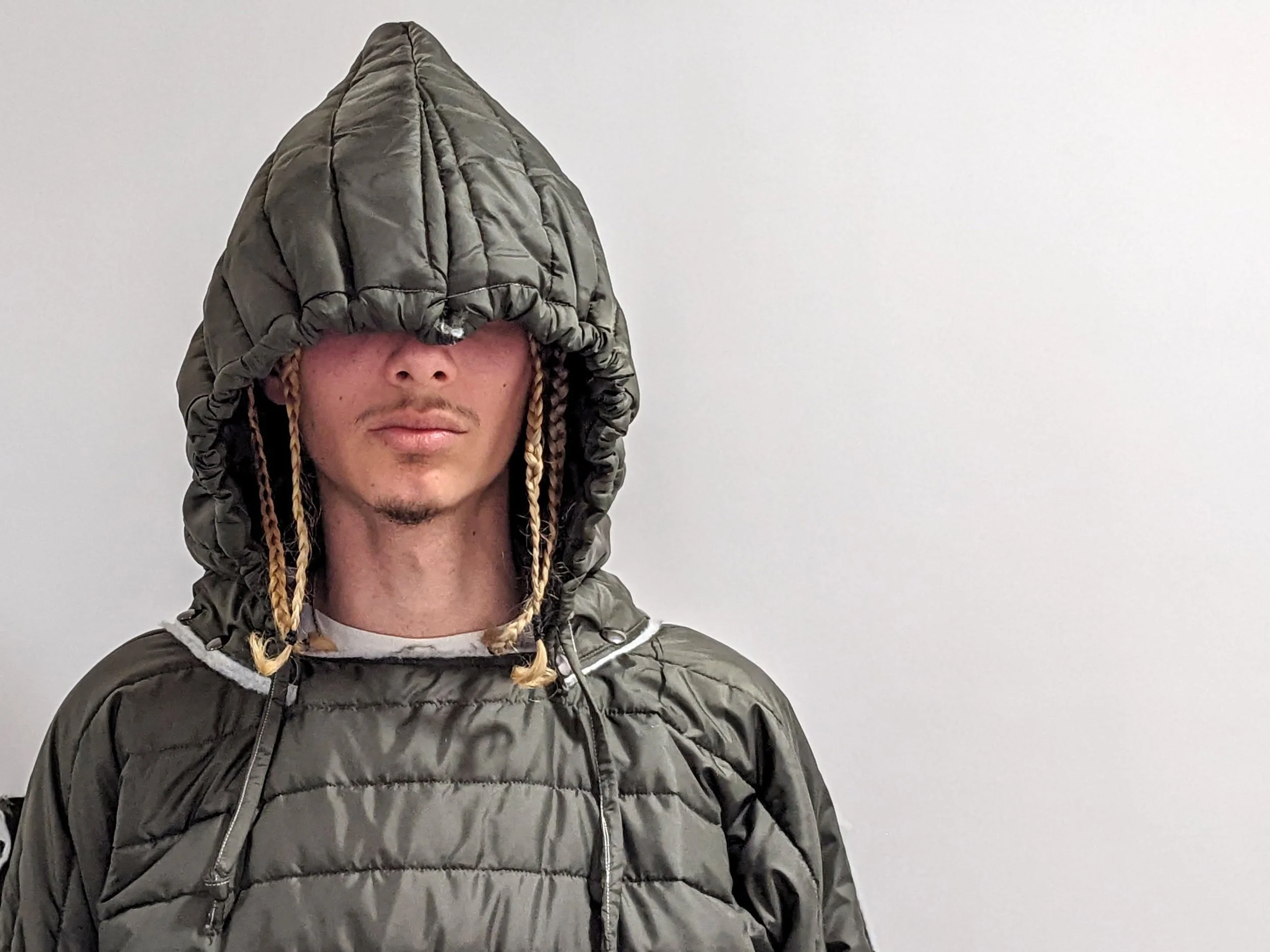
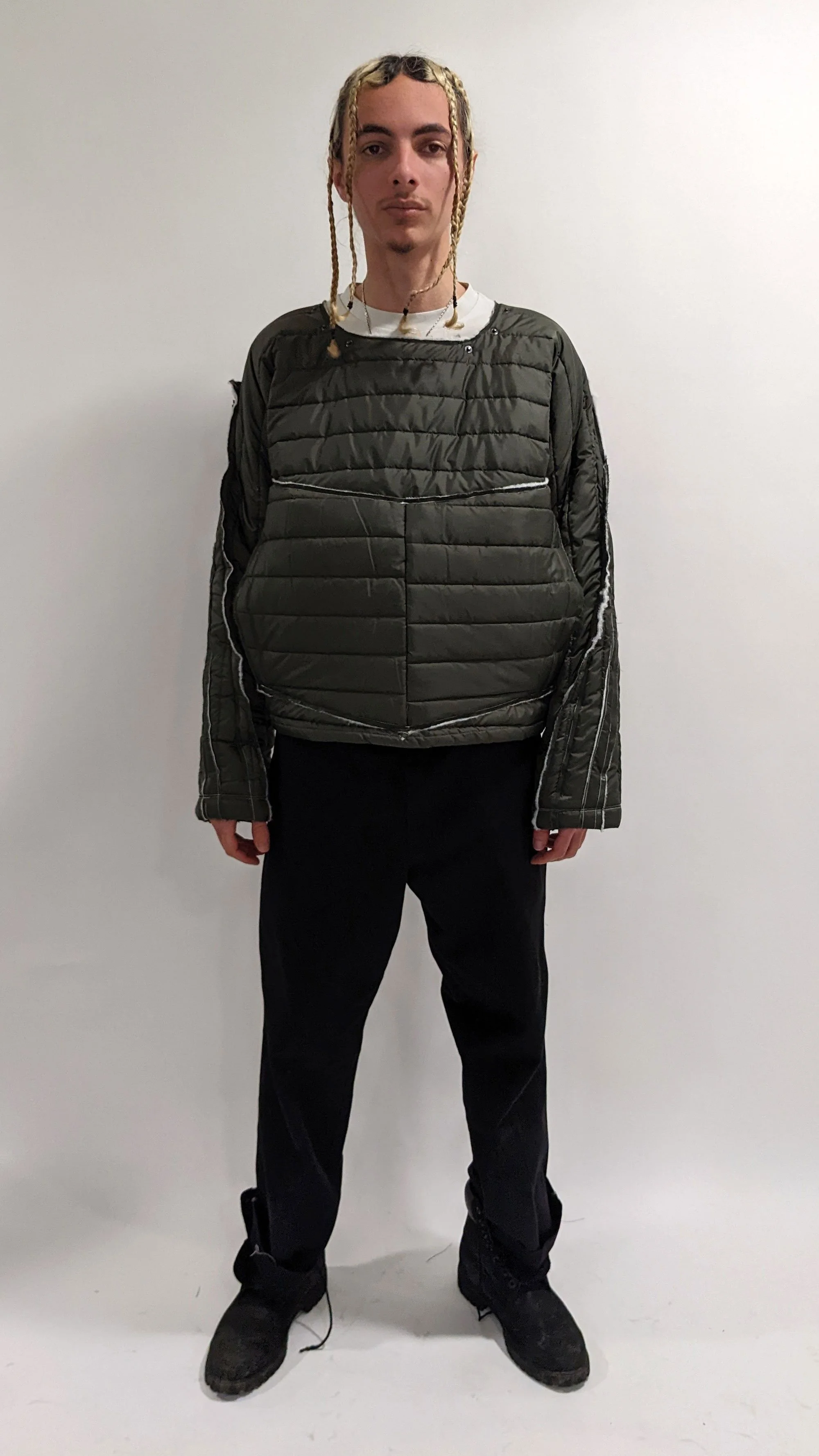
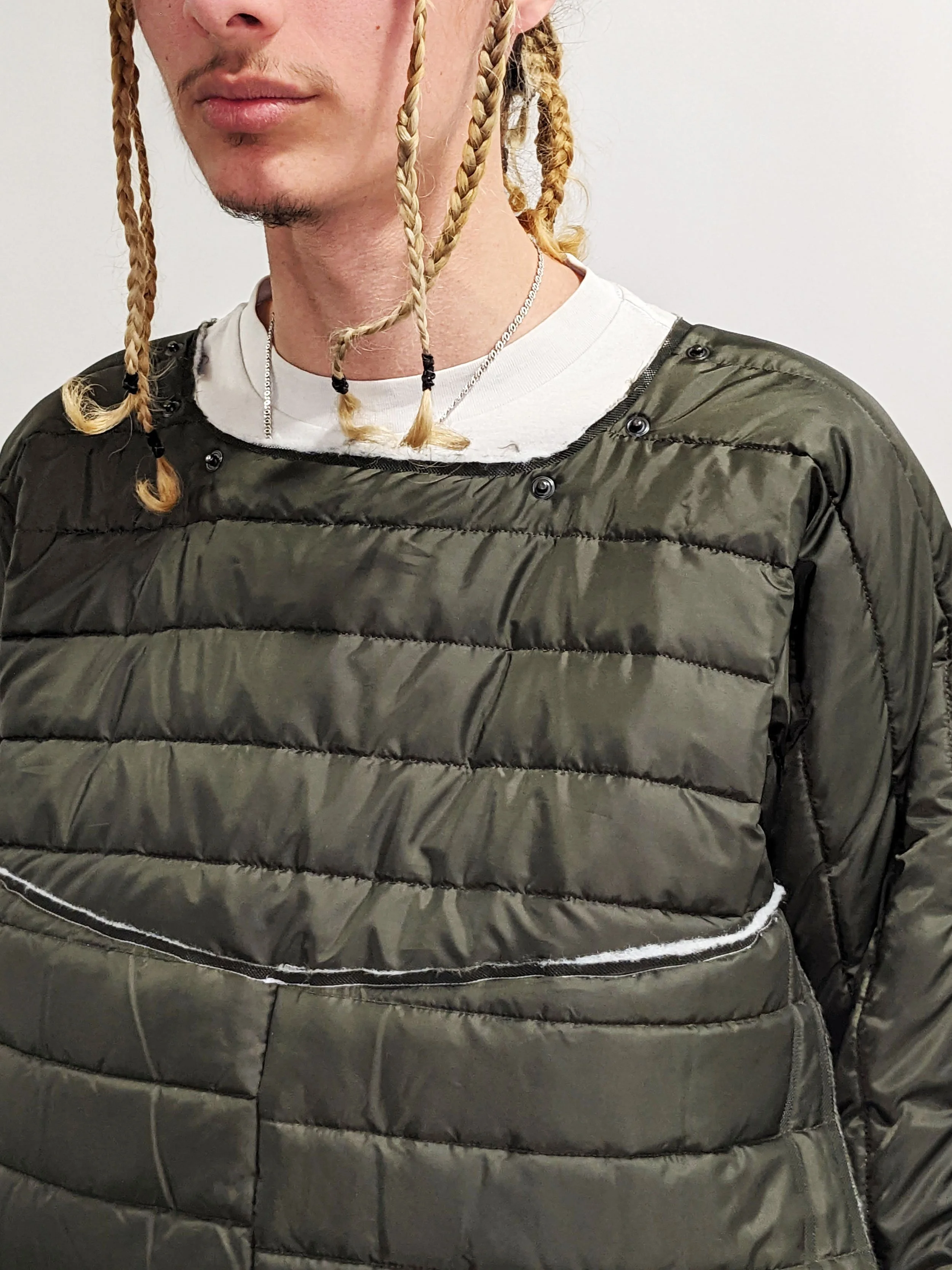
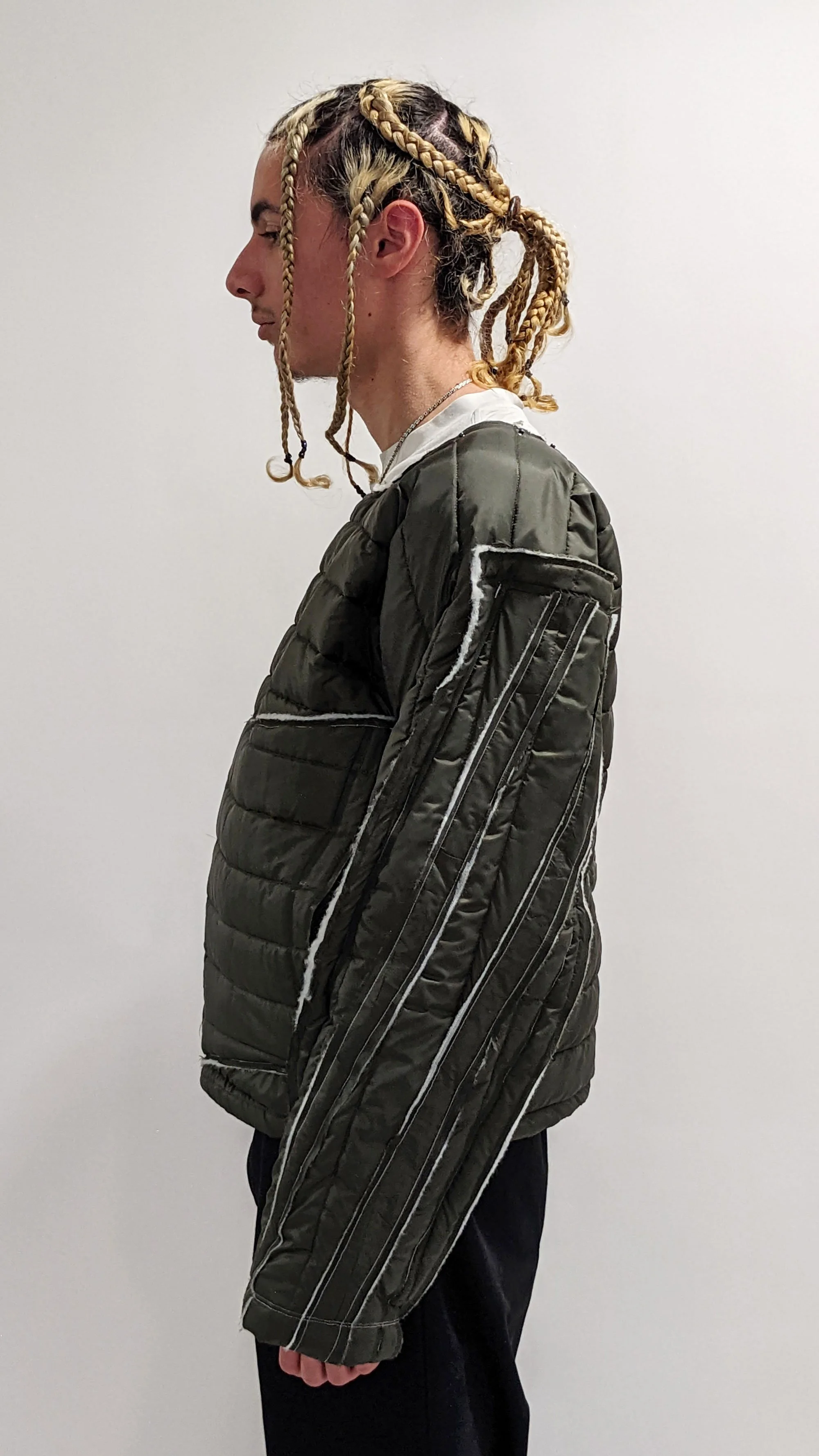
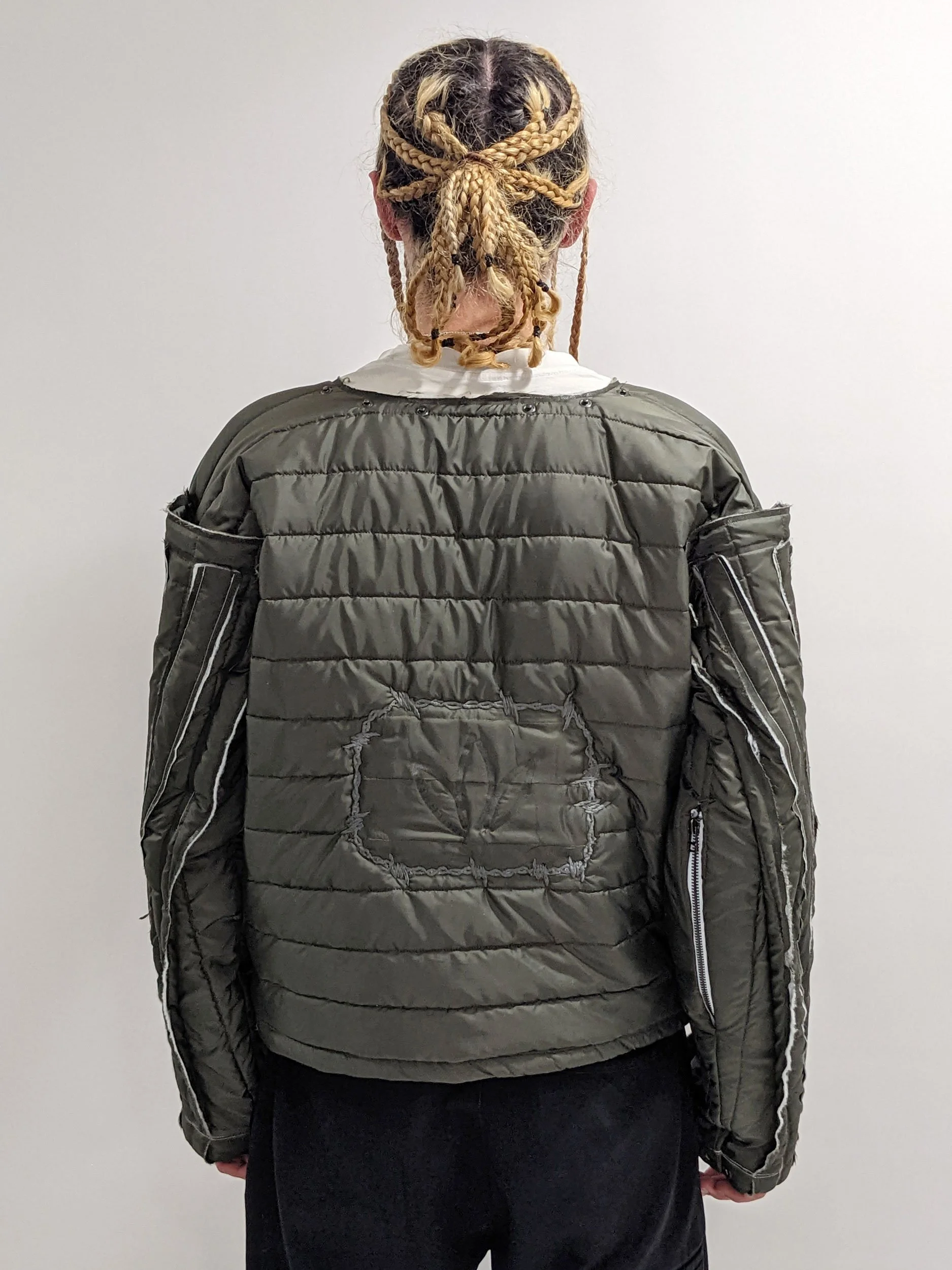
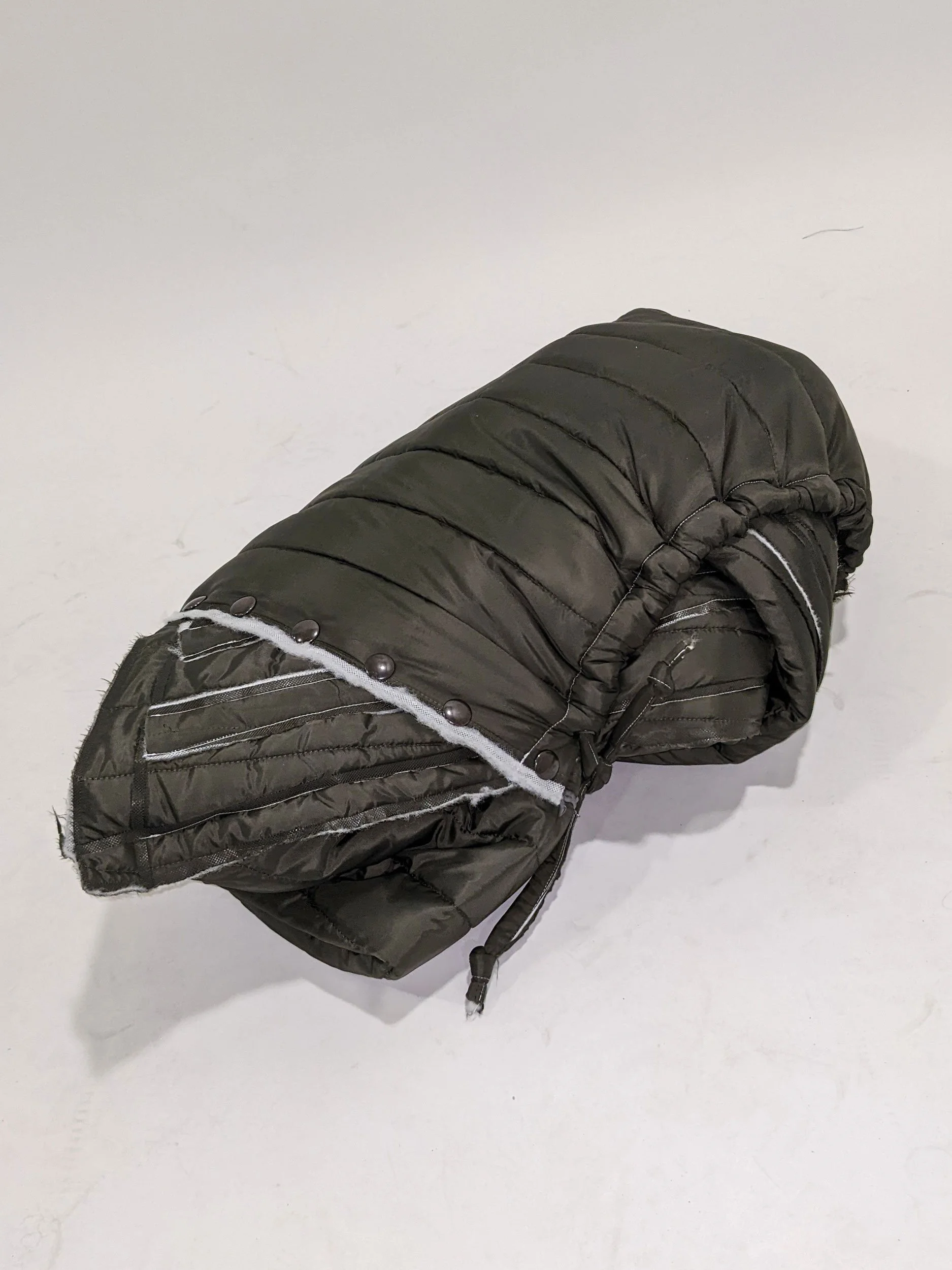
final shoot


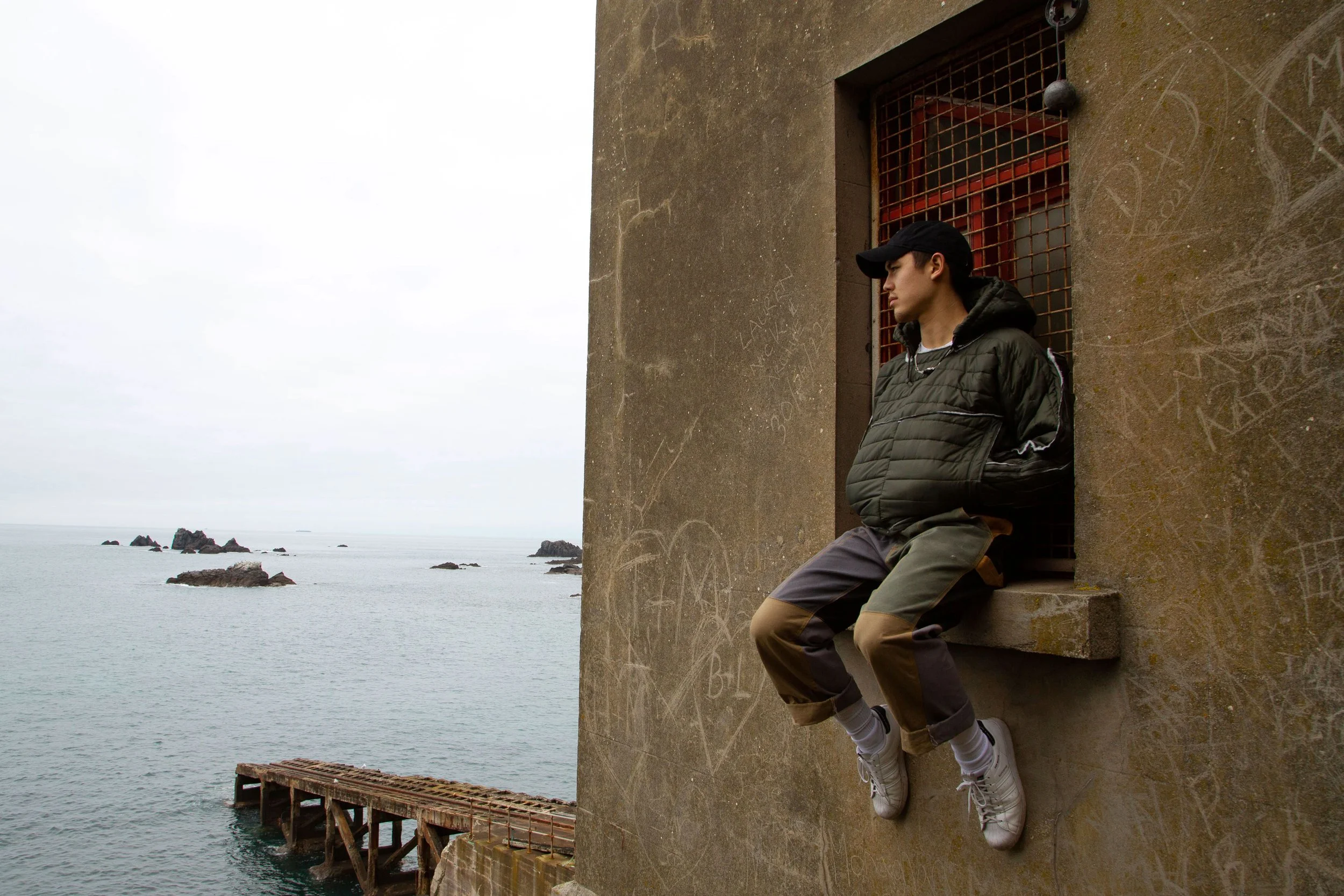

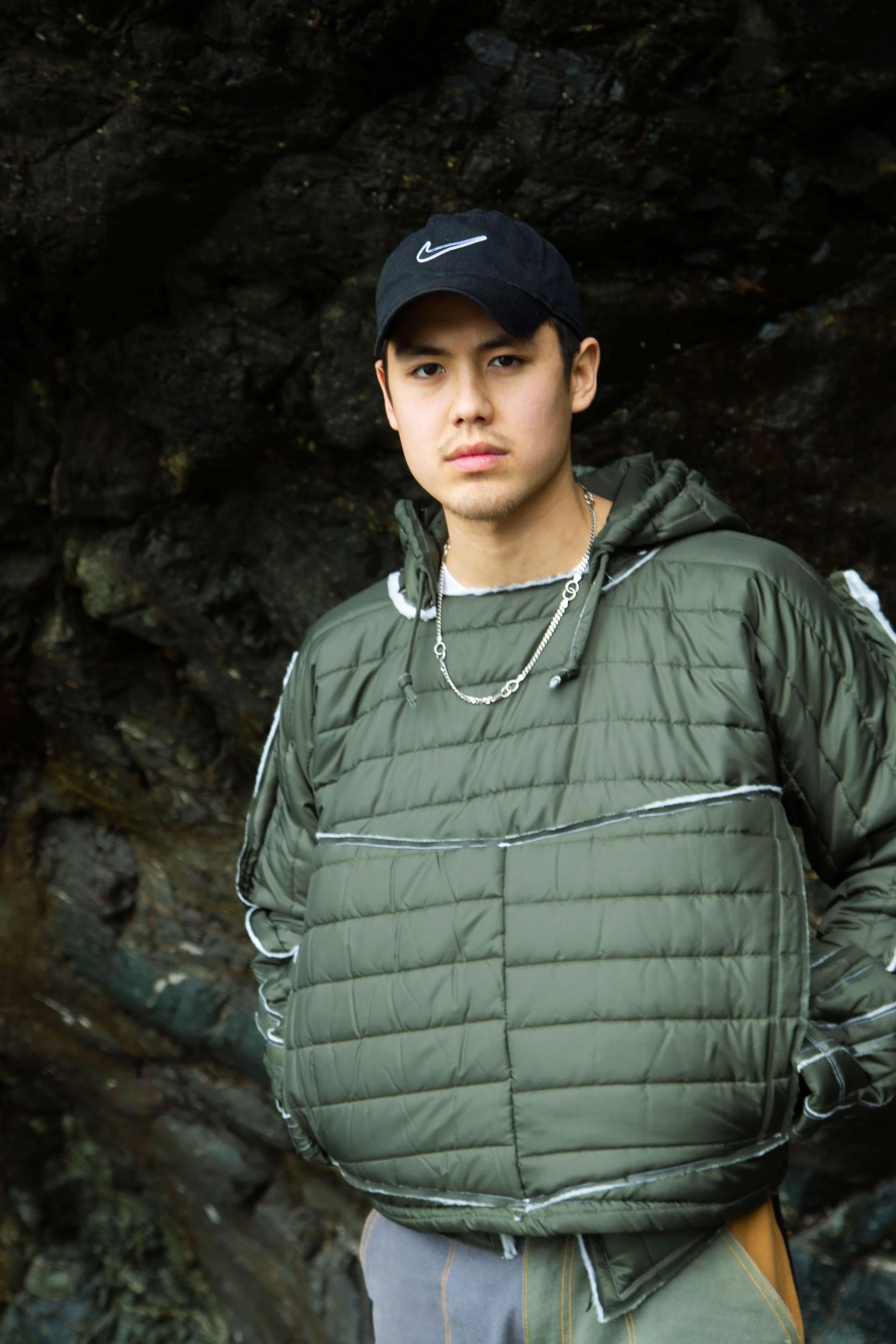
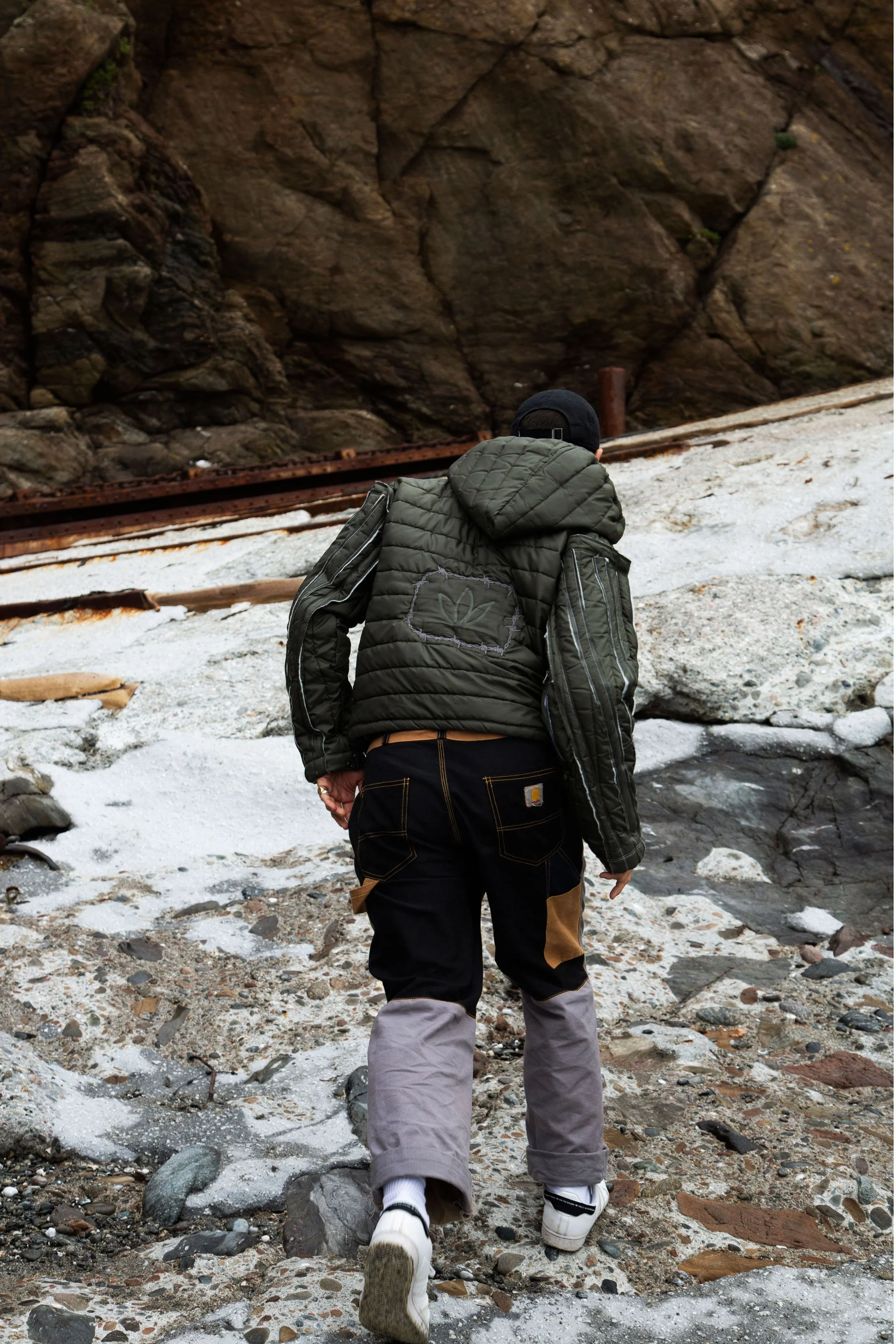

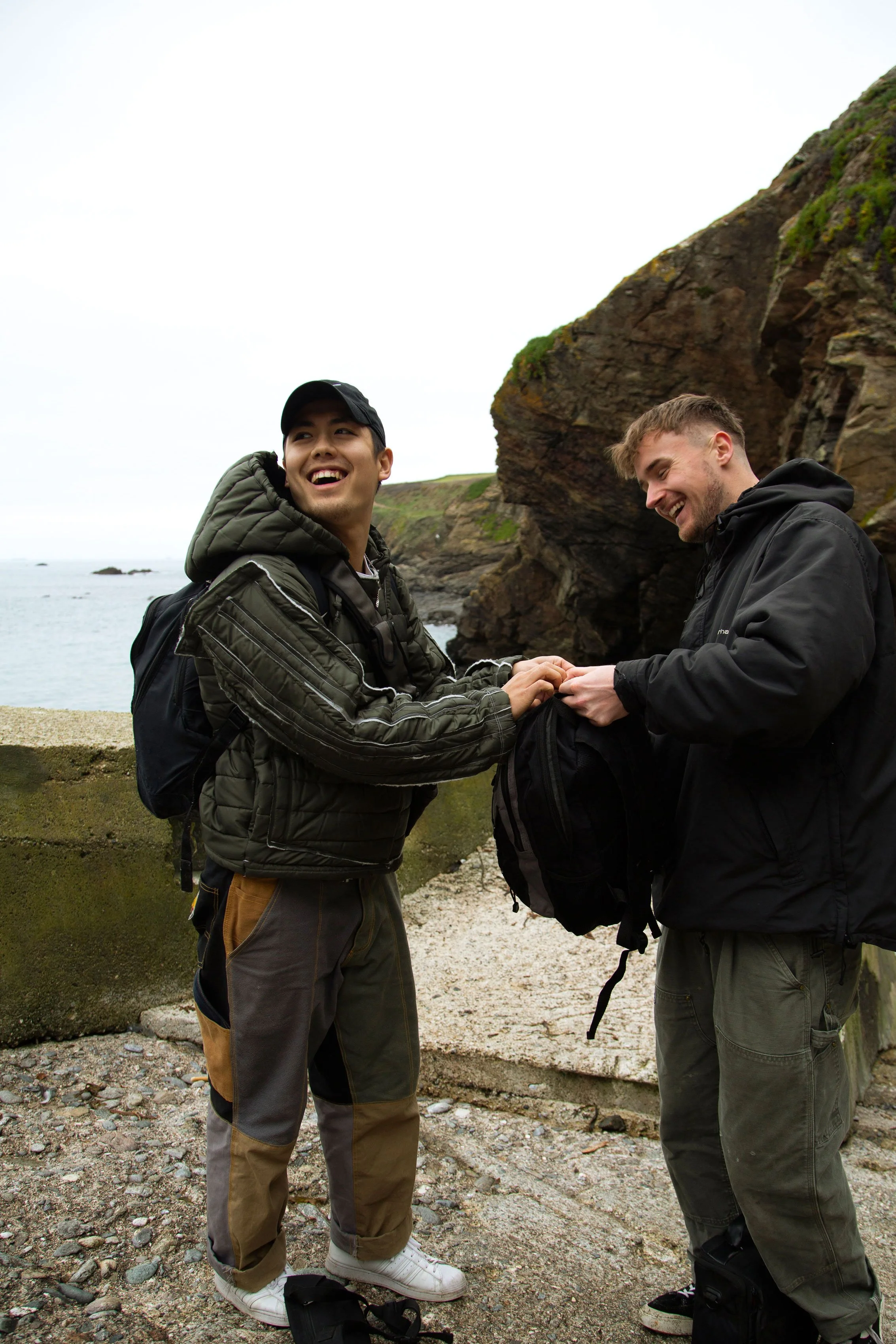
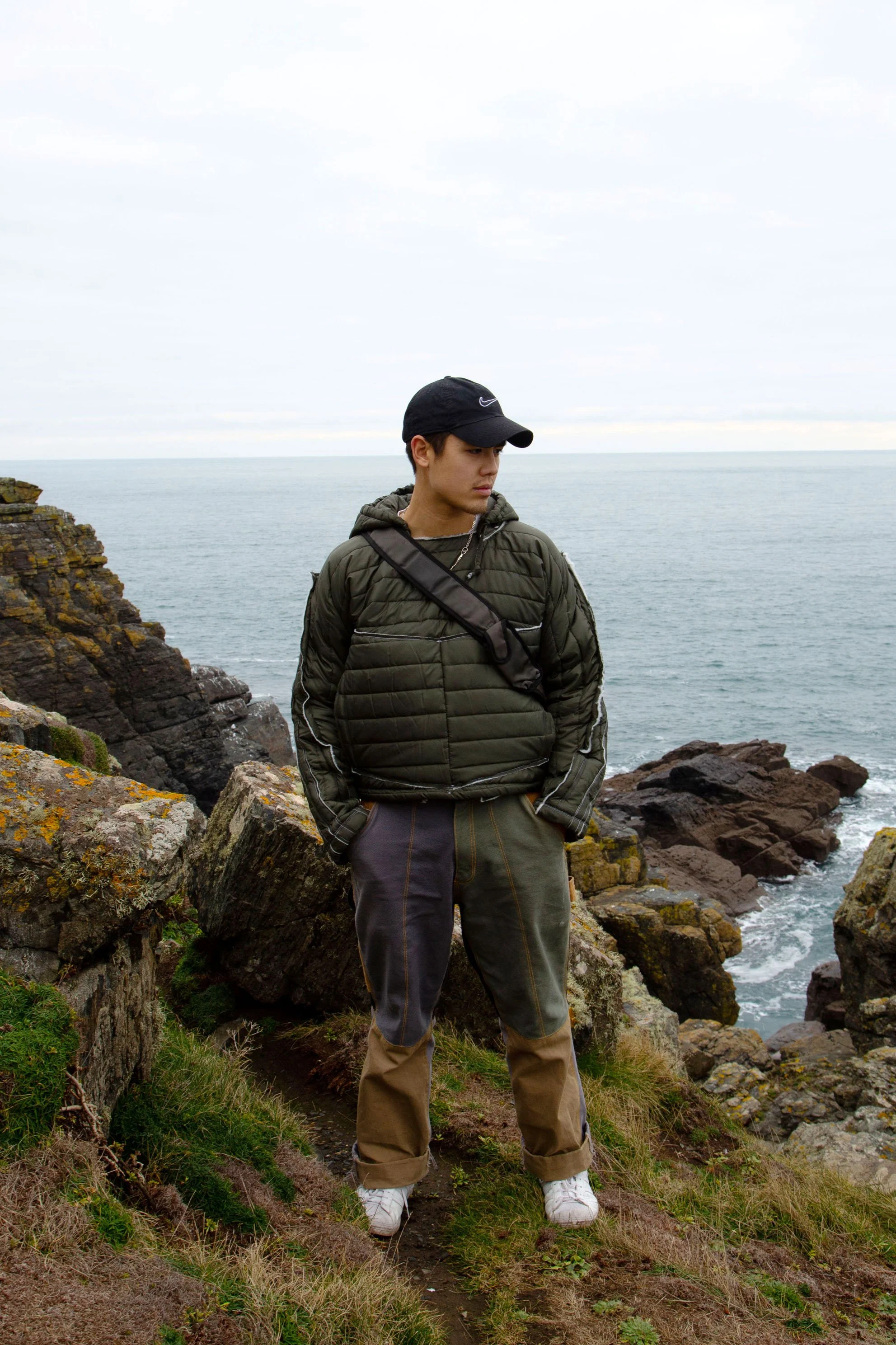



